How This Manufacturer Used Data to Increase Efficiency and Cut Costs This is what happens when machine learning comes to the factory floor.
By Marty Jerome
This story appears in the April 2016 issue of Entrepreneur. Subscribe »
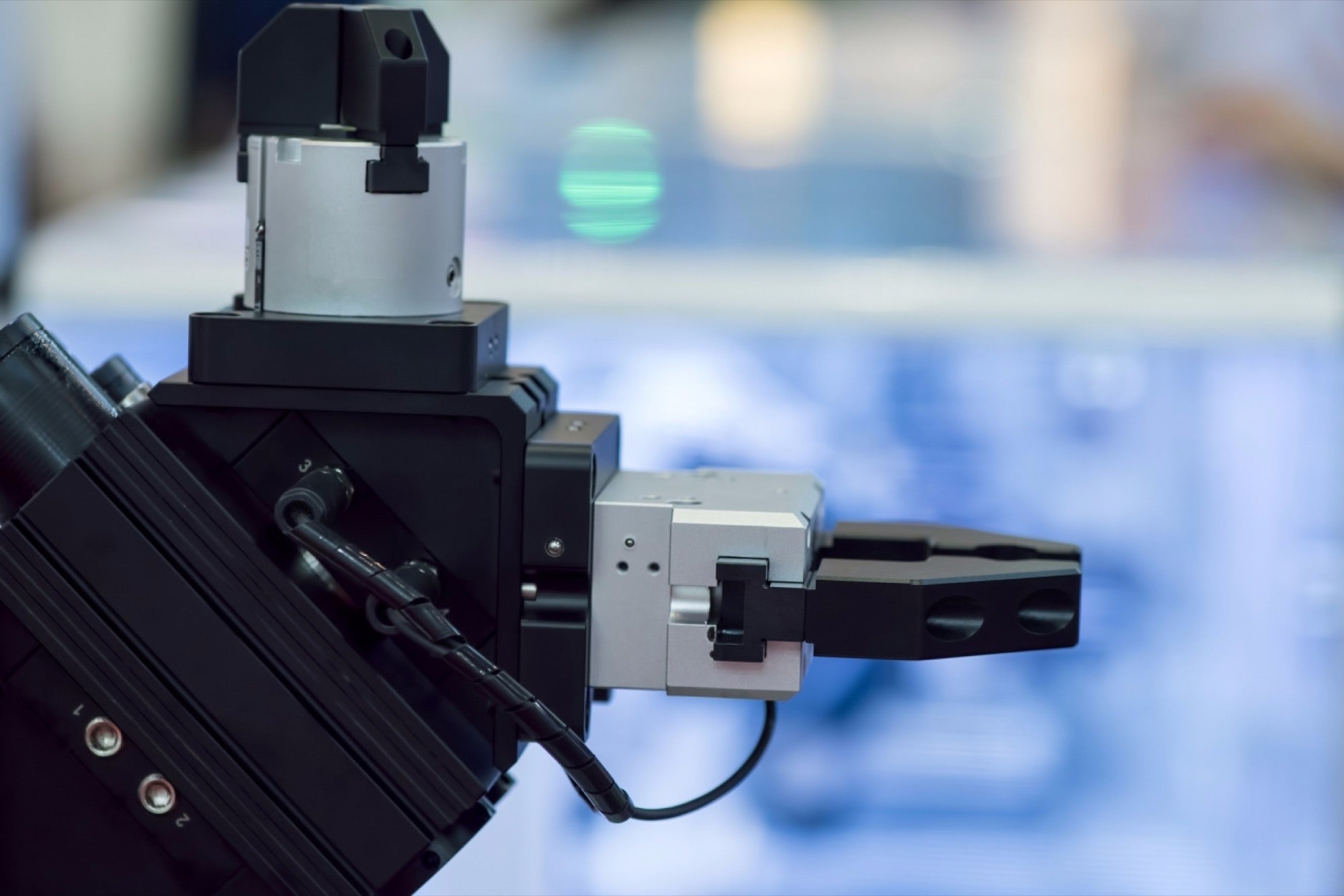
Inteva Products, a multibillion-dollar global manufacturer of auto parts, wanted to improve its products and sniff out manufacturing inefficiencies. So it ran an experiment: It hired Sight Machine, a 4-year-old San Francisco-based company that turns complex workplaces into crunchable data. The system works like this: For any part of a factory that Sight Machine wants to monitor, it sets up cameras and sensors and finds ways to pull in live feeds from any internet-connected devices, right down to a shop's HVAC system. Then the startup's software takes over -- pairing the data it's picking up from the cameras (say, how quickly employees are moving) with everything else it's learning -- to find out when and why production is lagging. "People making cars, shoes, drugs -- they all want to know what's wrong with their operation, and our software can tell them," says Sight Machine's CEO, Jon Sobel, a veteran of Tesla and Yahoo!
Inteva did a trial run to see if Sight Machine could identify ways to reduce the amount of scrap coming off the production line. It was a success, says Inteva CIO Dennis Hodges. He won't say how much he saved, but consider this: Sight Machine costs $50,000 to $100,000 to set up, plus a monthly subscription fee. To justify the cost, the savings have to be real. Now Inteva is expanding its use to see if the startup can help improve Inteva's injection-molding process. The data awaits.
The rest of this article is locked.
Join Entrepreneur+ today for access.
Already have an account? Sign In