How To Reduce Shrink With a Manufacturing Execution System An MES is a data hub that provides information for action throughout the plant
By Scott Sexton
Opinions expressed by Entrepreneur contributors are their own.
You're reading Entrepreneur Asia Pacific, an international franchise of Entrepreneur Media.
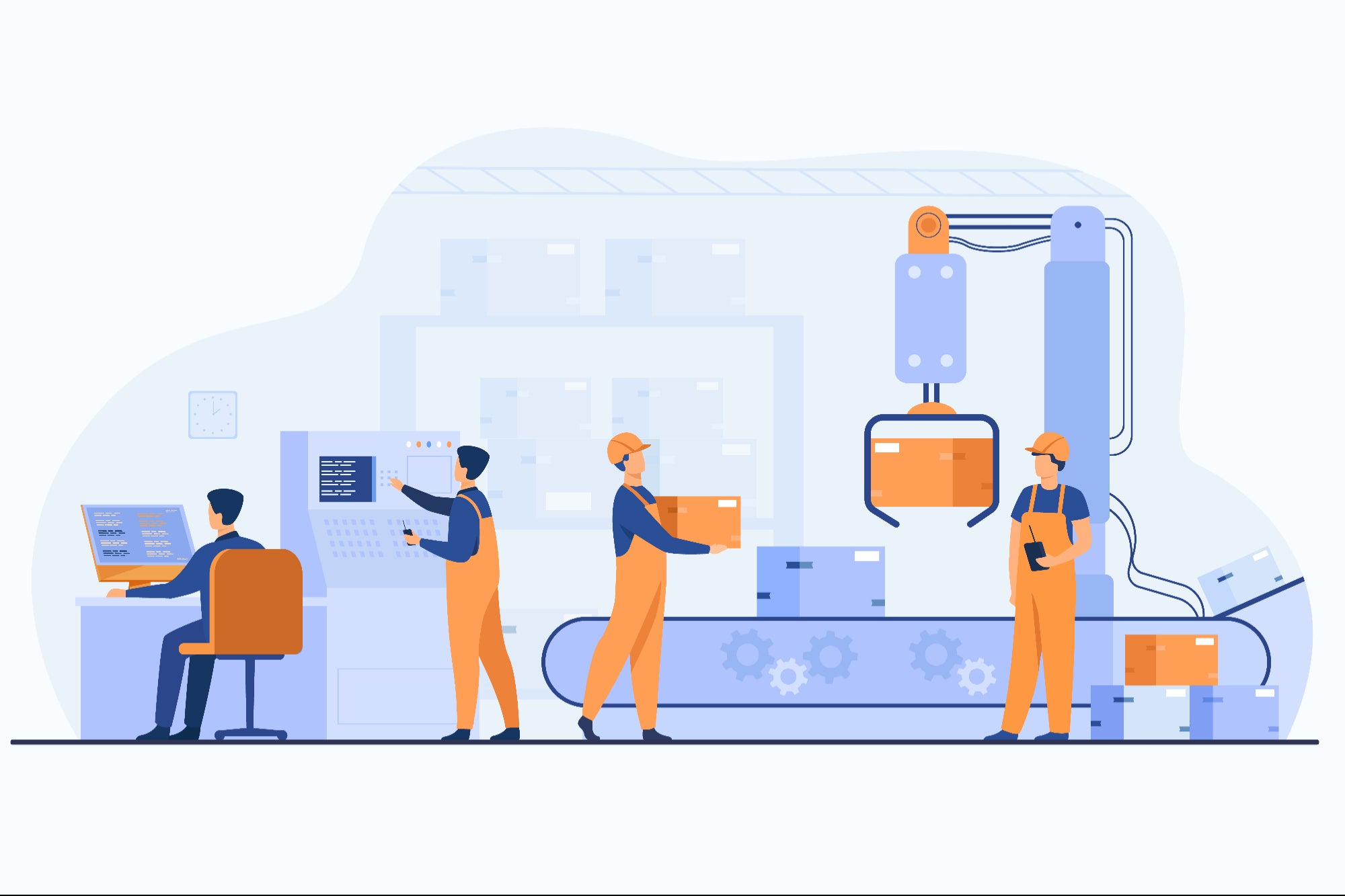
Oftentimes, a plant's potential is unlocked by simply reducing dairy liquid shrink, improving cheese yields, or recapturing material left on the production floor. To accomplish this efficiently and effectively, a plant needs to be able to efficiently collect data directly from the production floor and apply real-time feedback in order to make timely adjustments to batches. All these are made possible with the help of a manufacturing execution system (MES).
An MES is a data hub that provides information for action throughout the plant. Its real-time data intelligence capabilities create a communication layer between the systems executing the dairy plant's processes and the enterprise resource planning (ERP) that reports financial results. The ultimate goal is to help complete production and provide real-time insights into plant performance, enabling managers and users to improve the results.
MES plays an important role in dairy manufacturing. Below mentioned are four impactful ways in which an MES helps optimize processing to reduce shrink:
Gain full visual of processing
MES provides an easy view to determining the correct process for analyzing the data compiled at the weight and component level throughout production. With this thorough analysis, you will have complete visibility into vessels and outputs to determine your actual mass balance and yield. Mass balance and yield are differences between making and losing and are vital to efficient plant operation.
By identifying your key performance indicator (KPI) and benchmarks and measuring your plant's mass balance consistently, you'll be able to compare expectations to results and quickly and automatically identify discrepancies. Plants that utilize the resources of an MES have the benefit of this complete visualization. By gaining this capability, troubleshooting problems get quick and efficient without having to search through large amounts of data.
Track losses during cleaning
Ever considered how much shrink or loss occurs during the cleaning process? With an inefficient clean-in-place (CIP), one dairy plant can probably lo valuable product by simply letting it go down the drain.
Implementing an MES to monitor processing will ensure optimized and efficient ingredients management, even during the cleaning process. An MES interfaces with strategically placed sensors and monitors throughout production lines. Key people will be alerted if and when set parameters are triggered, from excess solids in a wastewater line to insufficient chemical utilization or temperature control during CIPs.
Manage recipes
Above all, batch recipes are crucial to producing a consistent product with perfect mass balance. Once the perfect recipe is discovered, it is essential to maintain a repeatable process through MES monitoring and tracking.
An MES gives precise knowledge of all the devices affecting the intricate measurements required for recipe management – down to the smallest component of the batch. Envision knowing where all the butterfat, protein, and other components are lost.
The recipe control also manifests improved operations for a cheese plant through cheese yield. The MES system digitizes the make sheet on the floor and essentially links to their plant's actual cheese yield. One can fully identify causes in yield variations from temperature to cut time to any other data captured in production.
Making more product through less OEE and visual factory
Not only does an MES help reduce loss with improved recipe management, but also offers the advantage of running overall equipment effectiveness (OEE) on the plant's key processes and equipment. OEE provides insights into whether lines or vessels are running and operating at benchmark speed, in addition to revealing any potential shrink and yield loss in the production lines.
OEE is the overall scorekeeper of any units within an entire plant's performance. For example, if the goal is to have 85 per cent OEE on a packaging line and the current score is 75 per cent, then there is a definite need to review the cause. OEE gives complete visibility into line performance to identify any problems, whether quality, speed, or overall availability. Furthermore, it determines if there is a maintenance issue, an unexpected downtime, or a possible processing issue causing loss.
Additionally, plants with remote visibility enabled through MES and focusing on OEE will prevent inefficiency through sub-optimal batches and rework without necessitating on-site monitoring of the process.
Further driving plant efficiency, visual factory is a valuable component of an MES system. With a swipe or click, one can get a complete, real-time view of the plant and processes in a much more powerful method than just an HMI screen. Visual factory means data from every measurement – from PLCs and SCADA systems down to a granular level – is available with an easy-to-use interface for any period back to ten years. Imagine quickly completing a root cause analysis when data is readily available and subsequently identifying why a specific batch does not meet quality or yield expectations.
It happens every day in any plant – losing track of product or making the goal of optimizing efficiency and profitability a compounding and frustrating situation for the dairy plant operations. Therefore, MES provides many long and short-term benefits as well as strategic and tactical benefits, including more rapid time to volume, improved yields, lower operating costs, increased compliance.
With better-automated solutions, any plant can significantly improve visualization of all the data in the manufacturing process, monitor systems, help reduce overall waste and provide proactive alerts to production issues.