Automating Growth In The Automotive Market DCM is supplying castings across all segments in automotive market
You're reading Entrepreneur India, an international franchise of Entrepreneur Media.
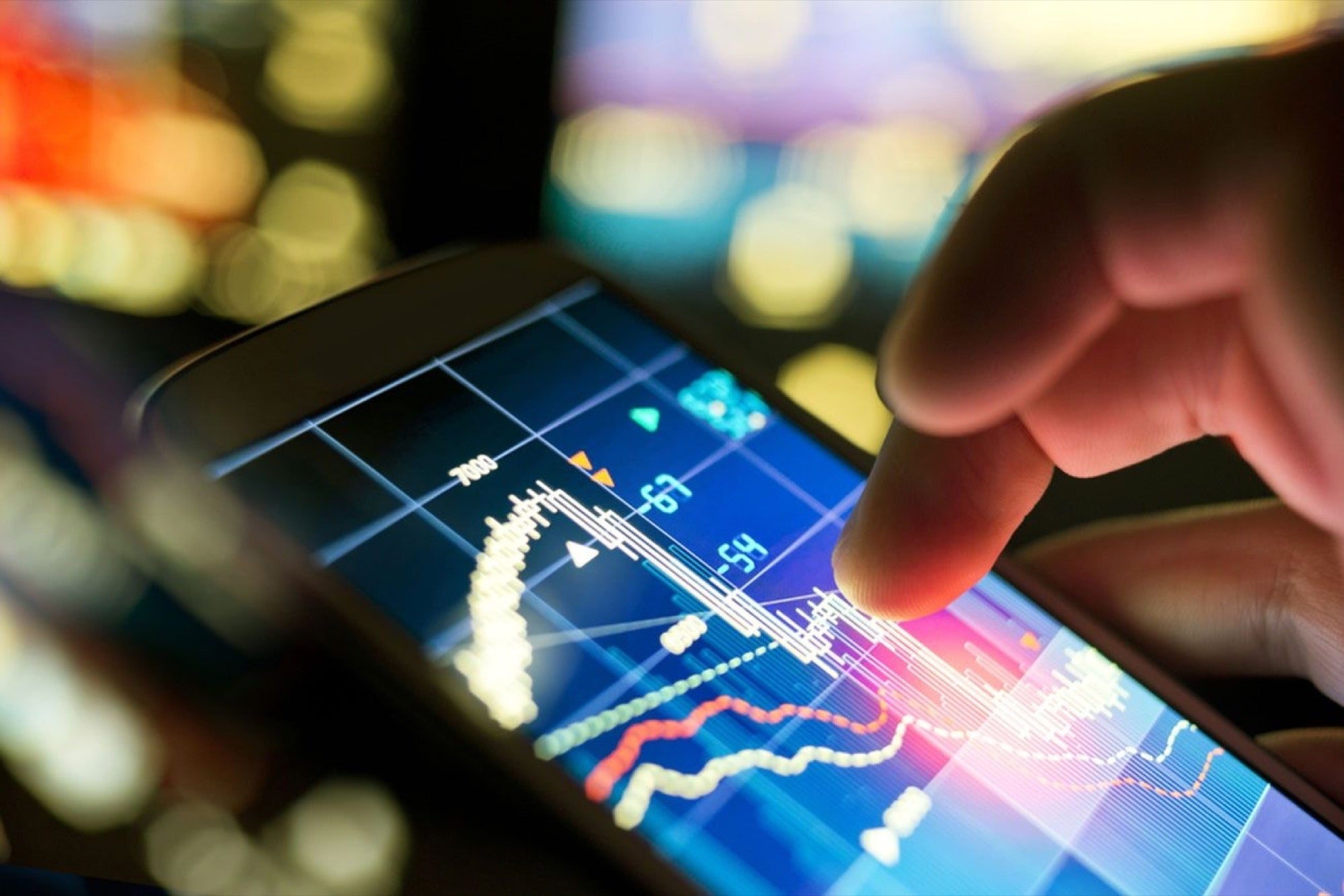
Punjab-based DCM Engineering Products (Unit of DCM Limited), has been a leading manufacturer of engine blocks and cylinder heads, Sumant Bharat Ram, Executive Vice Chairman, shares with Entrepreneur how investing in IT has paid great returns for the company.
Tell us about the inception of DCM Engineering and what have been the major milestones?
The origin of the DCM dates back to 1889, when Delhi Cloth & General Mills was established. Over the years, the DCM Group became one of India's largest conglomerates. Consisting of a large number of companies and divisions, the group is reputed for their product quality, dynamism and business integrity, along with their quick response to changes in the environment. One of the main reasons for the group's success is its focus on technology and quality.
DCM, headed by Dr. Vinay Bharat Ram, covers the activities in the areas of automotive engineering products, information technology, cotton yarn and real estate. It set up Grey Iron Foundry in 1977 with a capacity of 17,000 mtpa (metric tons per annum), as a division of DCM Limited. Currently its capacity is 72,000 mpta.
DCM is supplying castings across all segments in automotive market: car, multi-utility vehicle, tractor, light commercial vehicle, heavy commercial vehicle and earth moving equipments. In domestic market, it is associated with Maruti Udyog, Hyundai Motors, Mahindra & Mahindra, International Tractors Limited, Ashok Leyland, Eicher Motors, Escorts, Swaraj Mazda, JCB India, Force Motors, Simpson & Co and many more. Its association with international customers includes Perkins Motors.
How has technology fuelled the growth of DCM Engineering?
Technology has played a major role in growth of DCM Engineering. From automatic sand mixing to automatic core, molding machines to automatic fettling operation with accurate, high precision machines to lower human interference with real time data processing, company is known for a lot of things. This has increased volume and efficiency, while maintaining quality and competitive pricing. Our facility is equipped with the state-of-theart foundry technology to ensure unrivaled quality, faster turnaround and lower costs. We are equipped with siamese tooling capability, MAGMASOFT® simulation, GOM 3D White Light Scanner, press pour, Lampe and Loramendi cold box sand mixing and distribution system, Maus Machines, Automatic Core Cell by Loramendi.
In which year did you adopt IT solutions and how it has turned around the growth of the company?
Oracle was the solution used before 2005. SAP ECC 5 has been implemented in 2006 and later it upgraded to ECC 6.0 EHP6. As a strategic partner, Fujitsu has helped DCM Engineering to procure SAP S/4 HANA licenses.
How is the company readying itself for future growth?
We are diversifying in different business segments to propel future growth in automotive industry.
Effect of IT
>>Automated shipment process for outward and inward entries, vis-à-vis daily balance sheet and profit statement
>>Real time updation of production data through GE-IGS, GE-Historian, BDC in SAP including weighing bridge and manpower management
>>Concurrent generation of salary through FORM 16 for employees and vendors in SAP.
>>Discrete planningand non deterministic planning at core making and melting furnace.
>>Quality system for complex foundry process in compliance with TS 19649
(This article first appeared in the Indian edition of Entrepreneur magazine (October 2016 Issue).