Design Thinking is to Innovation what Six Sigma is to Quality This iterative process relies on systematically shaving off waste from the system, resulting in a leaner process, with hopefully a better outcome
By Dr. Pavan Soni •
Opinions expressed by Entrepreneur contributors are their own.
You're reading Entrepreneur India, an international franchise of Entrepreneur Media.
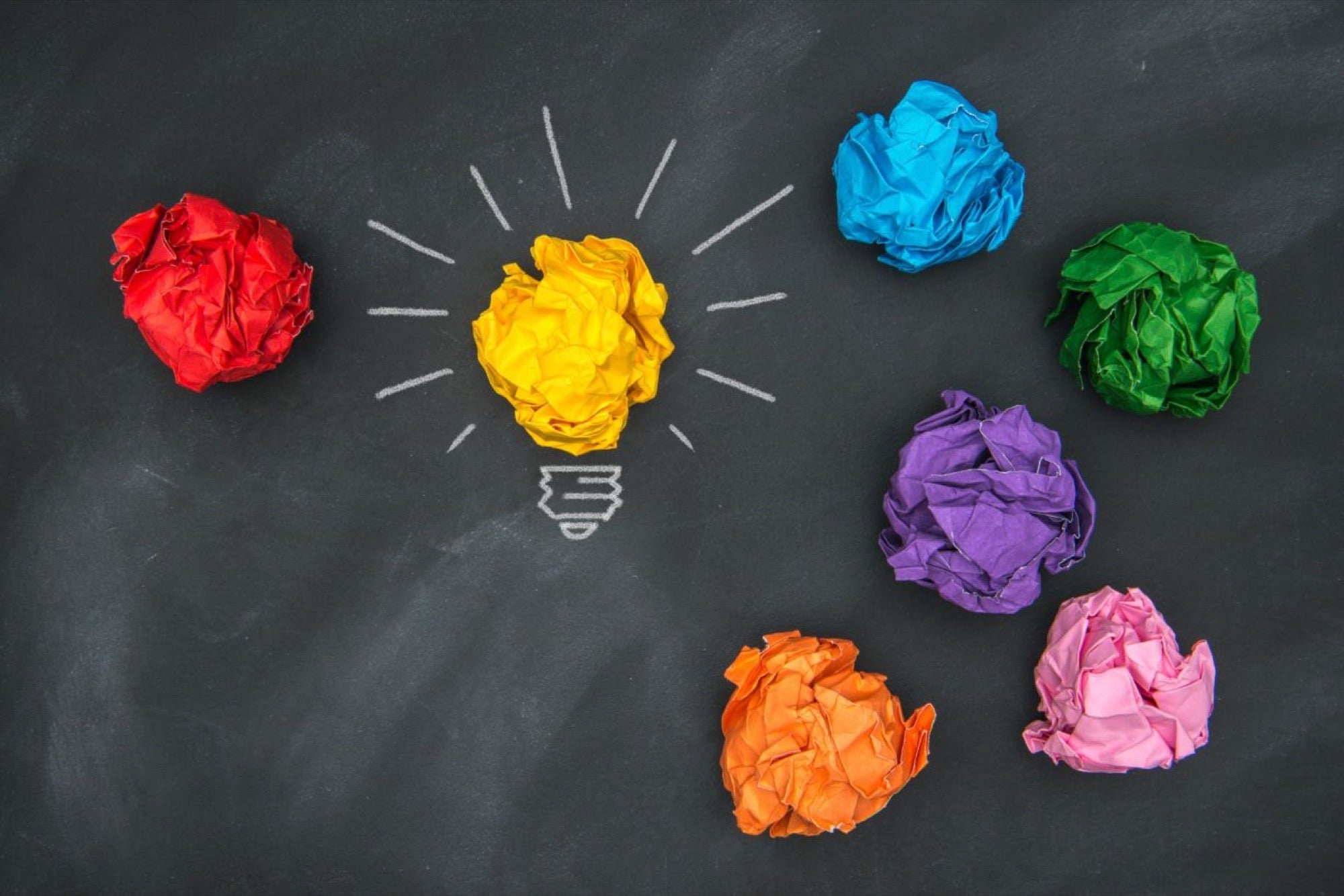
Imagine you are in the 1960s, in any part of the world, and you are talking about product quality. For one, it's not a good conversation starter, and secondly, the quality was associated with the person who makes the product and not the company, let alone the processes. Then came the Japanese, who with their unitary focus on process quality taught, first the Americans and, then, rest of the world that a quality output can indeed be engineered much like the products. Toyota, Sony, Honda and scores of Japanese firms soon became the gold standard of quality and efficiency, apart from utilitarian designs, in their respective fields and brought in a revolution in manufacturing and then into the services industry.
The Americans dubbed some of these practices under the rubric of Six Sigma, and the likes of Motorola, General Electric, and Allied Signals, amongst others, exported the methods to rest of the world. Today, Six Sigma and its derivatives have become a part of the vocabulary of the quality teams in manufacturing and services companies alike. Six Sigma has emerged to become the repeatable, reliable, and scalable way of managing process and product quality.
The state of innovation today is akin to the state of quality in the 1960s.
Innovation is still, very, unfortunately, deemed as the domain of the gifted, the well-endowed, and the inspired (this one may be true), and no so much of a matter of processes, routines, and practices that can be tamed and improved. Worst still, a large section of practising managers and academics refuse the come out of the shadow of their charismatic leaders, like Steve Jobs, Elon Musk, and Jeff Bezos and appreciate that innovation can be institutionalized. Can Design Thinking be the answer?
We don't have to suggest the approach as a panacea for any kind of innovation-related issue, especially if it's regarding culture, but certainly, it can offer a great deal of discipline in the pursuit of innovation. But let's first revise Six Sigma.
The essence of Six Sigma, non-statistically speaking, is the DMAIC process, which stands for Define, Measure, Analyse, Improve and Control. This iterative process relies on systematically shaving off waste from the system, resulting in a leaner process, with hopefully a better outcome.
Figure 1:DMAIC Process of Six Sigma (Source: The Institution of Mechanical Engineers)
Design Thinking follows a similar iterative process. In the most widely adopted model, the one from Stanford School, Design Thinking comprises of five stages – Empathise, Define, Ideate, Prototype, and Test.
Figure 2: Design Thinking Process (Source: Stanford d.School)
Six Sigma was oriented towards ensuring process consistency and reducing waste, whereas Design Thinking started as a product innovation method. However, over time, these processes have morphed into general practices of improvement, beyond processes and product, respectively. Design Thinking, if practised with disciplined, can help solve some of the thorny problems e and beyond.
Though Six Sigma saw a wide-scale adoption soonest it hit the corporate shores, the same hasn't been the case with Design Thinking. There seems to be more of curiosity and buzz than actual adoption. Here, some of the practices that could potentially help scale the adoption of Design Thinking. These could also be possible departures from the ethos of Six Sigma, and hence worth a read.
Design Thinking is Not About Design, it's About Thinking
One of the common myths around DT is that it's all about design. Though the origin of DT has been from the domains of industrial and product design, the approach has since then far moved from the context and is amicable to solve almost any problem. Think of the outcome of DT as a simpler solution to a thorny problem, and not necessarily a great design. This notion also relieves one from the psychological pressure of being a designer-type. No specific skill, except the discipline of thinking, is required for when it comes to practising DT.
The focus is on thinking and not designing. It's about designing your thinking by adopting a systematic and systemic approach in place of a more common-sense laden, gutfeel driven one. Remember, it's only the systematic, methodical and rigorous approach that can possibly be scaled. DT offers you one.
Focus On The Subject, Not the Object
What really distinguishes DT from the traditional methods of problem-solving, such as TRIZ, Lateral Thinking, the theory of constraints, Six Thinking Hats, Mind mapping, etc., is that DT starts (and ends) with the user, and not the product or the process in question. So, if we were to improve a pen or innovate a new writing device, the starting point won't be the existing pen or the process of making the pen, but instead the very use of the pen. By adopting DT, it might so happen that the end result may not be a pen, but instead another means of expression adopted by the user.
The focus on the subject (the user or the customer), and not on the object (the product or the process) lowers the risk of over-engineering the product and the subsequent escalation of commitment.
Prepared to be Wrong, at Least the First Time
One of the common management dictums that stem from the quality movement is – "right first time'. But the underlying assumption of the right first-time ethos is that there's minimal discovery involved and that the process is reduced to a set of rules that need to be followed flawlessly. That may be true in a factory setting where most gains accrue from efficiencies. But in a studio, where uncertainties are galore and several unknowns are yet to be discovered, it's prudent to be "wrong first time', and wrong the second and the third time also, till you hit gold.
Being okay to be wrong the first time allows for rapid discovery and not labelling a person a failure. Unfortunately, lack of psychological safety at the workplace and personal courage makes it difficult to fail, even for once. That's why quality movements are more popular than innovation breakthroughs, they are by-design less risky.
Solve the Problem With the Customer, Not For the Customer
Ever wonder why the customer doesn't jump on your latest creation the way you would like her too? The problem is that your innovation is great in your head, and not in the mind of the customer. It's your job to excite the customer before she relents and pays (a premium) for your genius. Most engagements of seeking customer insights or market foresight are infested with guesswork and result in trying to convince a customer of what she never desired. What if the customer was with you all through the innovation journey, and not just as a recipient?
The systematic approaches of empathizing, prototyping, and testing engage the customer all long the concept to realization journey and it means that you are creating and commercializing almost in tandem. Needless to mention, this cuts down vital engineering and selling efforts, plus elevates customers' confidence while keeping your anxiety at bay.
Think With Your Hands, Together
While the process of DT may look sequential, it is nothing but sequential. It's highly iterative, flexible and adaptable to the context at hand. The key, however, is to try out new concepts as early as possible to avoid any escalation of commitment or amassing sunk costs. By thinking with your hands, you are essentially trying out how the ideas look and feel, and hopefully, together with your customers and key stakeholders. This helps you get a great deal of clarity on your problems/ concepts, and also help solicit otherwise sticky perspectives and knowledge from other experts.
The iterative, collaborative, tactile, and lucid approach of DT helps cull out wrong pathways early on and helps save precious efforts. Design Thinking can be the starting point of the fuzzy front end of the
innovation process and Six Sigma can take over from there on once most of the uncertainties are resolved.