More Reasons to Rethink Paper Records In this case study, RM Foods deployed an ERP system that helps it keep better track of inventory and financials than spreadsheets and handwritten paperwork.
Opinions expressed by Entrepreneur contributors are their own.
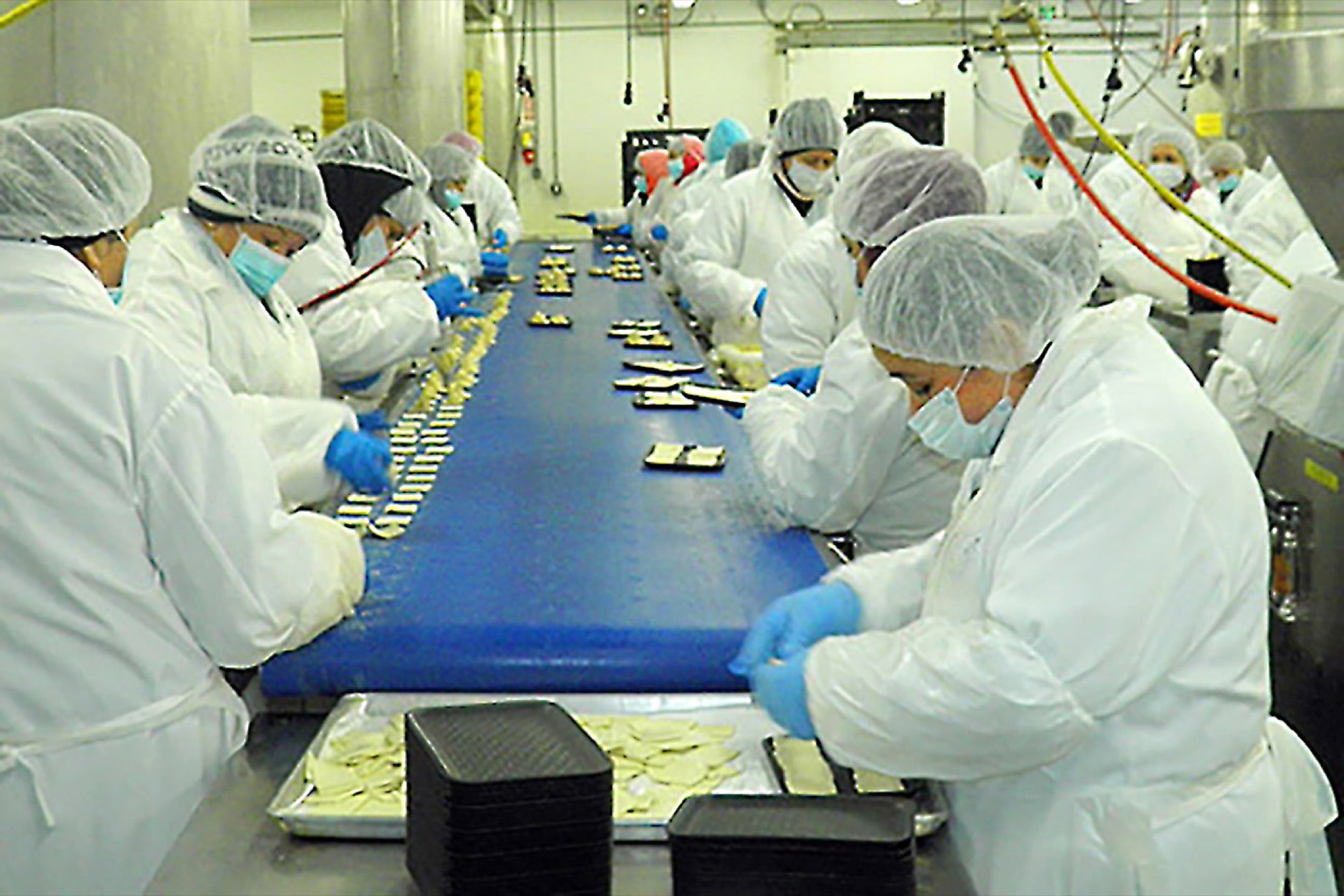
The Challenge: In early 2012, RM Foods, a Vernon, Calif.-based food distributor and contract manufacturer, was in an unsavory situation. Its parent company, Real Mex Restaurants Inc., had filed for Chapter 11 bankruptcy protection and shuttered more than 100 of its Mexican chain restaurant locations, from El Toritos, to Chevys to Acapulcos, across the U.S. That ate heavily into RM's distribution channel, and annual revenues fell drastically.
New president Michael Siegmund saw that the company needed to transform its business model. A big piece of that was changing how it managed financial and inventory data. Until then, the company used Microsoft Excel spreadsheets and handwritten paperwork to track orders, inventory and financials. Siegmund, who'd consulted for much larger food companies, knew that software programs could help RM keep more organized, accurate records. As it was, the company was having to store and keep track of bundles of hardcopy records. "We have an old trailer in the parking lot that now is literally full of (quality assurance) records," he says.
The Fix: In mid-2012, the company put out a request for proposal for an Enterprise Resource Planning system, software that integrates the management of information across an entire organization. Five companies submitted bids, and RM Foods selected a Sage ERP because it offered all of the features that RM needed at about "half the price" of other bidders, Siegmund says. RM spent about $1 million integrating Sage's ERP system and pays an ongoing maintenance fee.
About 75 RM Foods employees now have access to the ERP system, which the company uses to track financial accounting, warehouse management, manufacturing management, purchasing and asset management. In the past, RM employees would have to dig through paper records or individual computer documents when they wanted to check something. Now, they can retrieve data within seconds on their computers. They can easily build financial or inventory reports, gleaning better insights into company operations. "What this system allows us to do is gain efficiency in the gathering and processing of information," Siegmund says.
For example, in the past, when a contract manufacturing client sent in a recipe, it could take an RM employee many hours, even days, to input the recipe and give the customer a breakdown of ingredient prices. Tweaking the recipe could take many more hours. Now, the ERP system has ingredient information programmed into the system, drastically reducing the time it takes to input recipes and produce cost analyses.
That's just one example of many, Siegmund says, of how the ERP system saves time. Others include the easy sharing of information between employees in different departments and the data analysis tools and functionalities the system offers. Siegmund estimates the company saves $400,000, the equivalent of 10 employees, through just the time saved by using the ERP system. "I've had so many requests for financial information, because once you've been through bankruptcy, everybody wants to see your financials," he says. "Without the ability to generate the information by hitting a couple buttons on the computer, I don't think we could have survived."
Since deploying the ERP system last year, the company has grown from 117 to 250 employees. Annual revenue was $17 million in 2012 and is on track to reach $34 million this year.
The Takeaway: Using software that streamlines data management across an organization can reduce the paper trail and save valuable employee time.